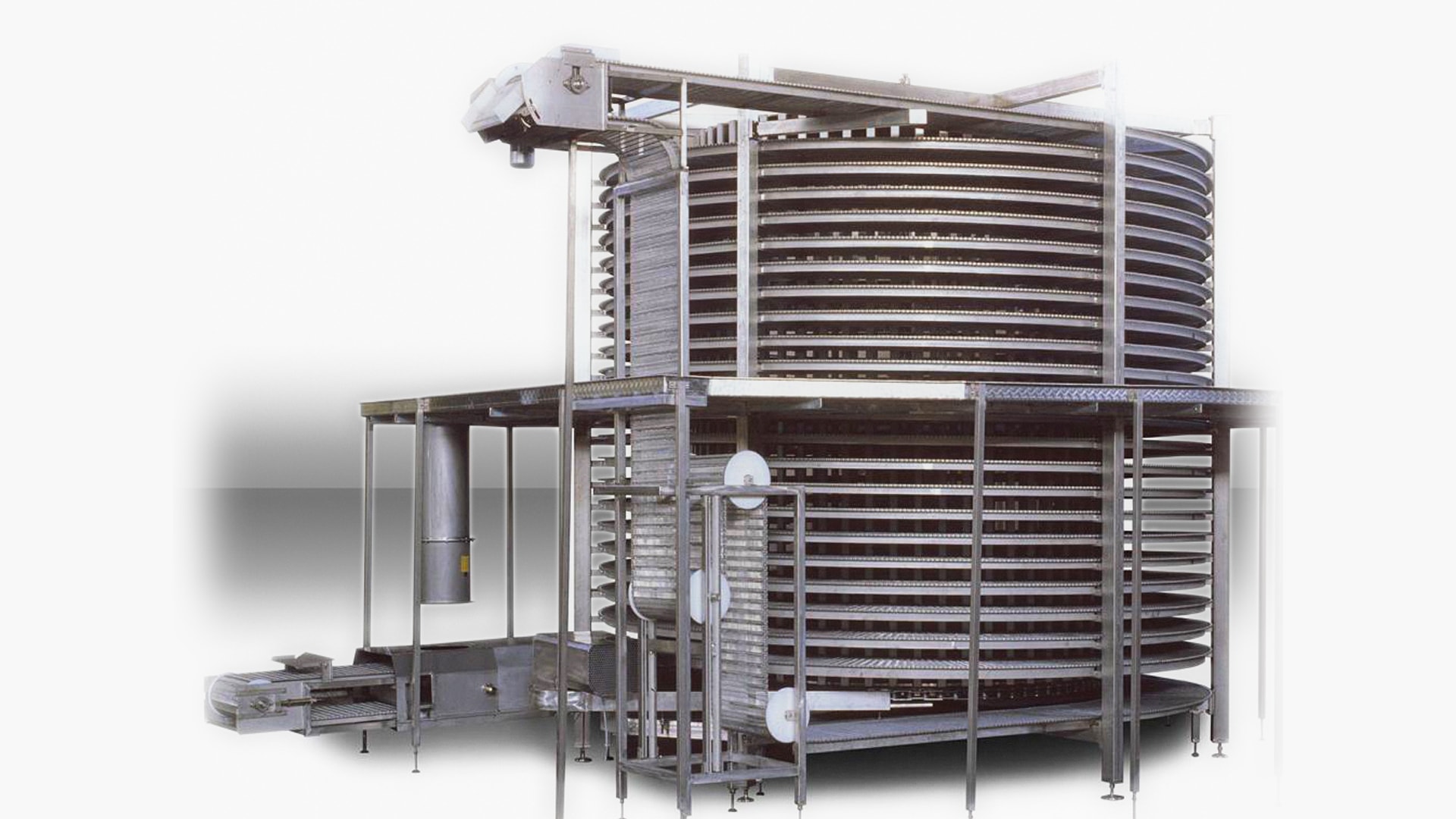
Spiral systems
Wide range of spirals capable of handling different packaged or loose food products.
Our range of spirals pasteurize, cool, refrigerate, cook and dry various food products. Each system is customizable to meet the customer’s technical specifications.
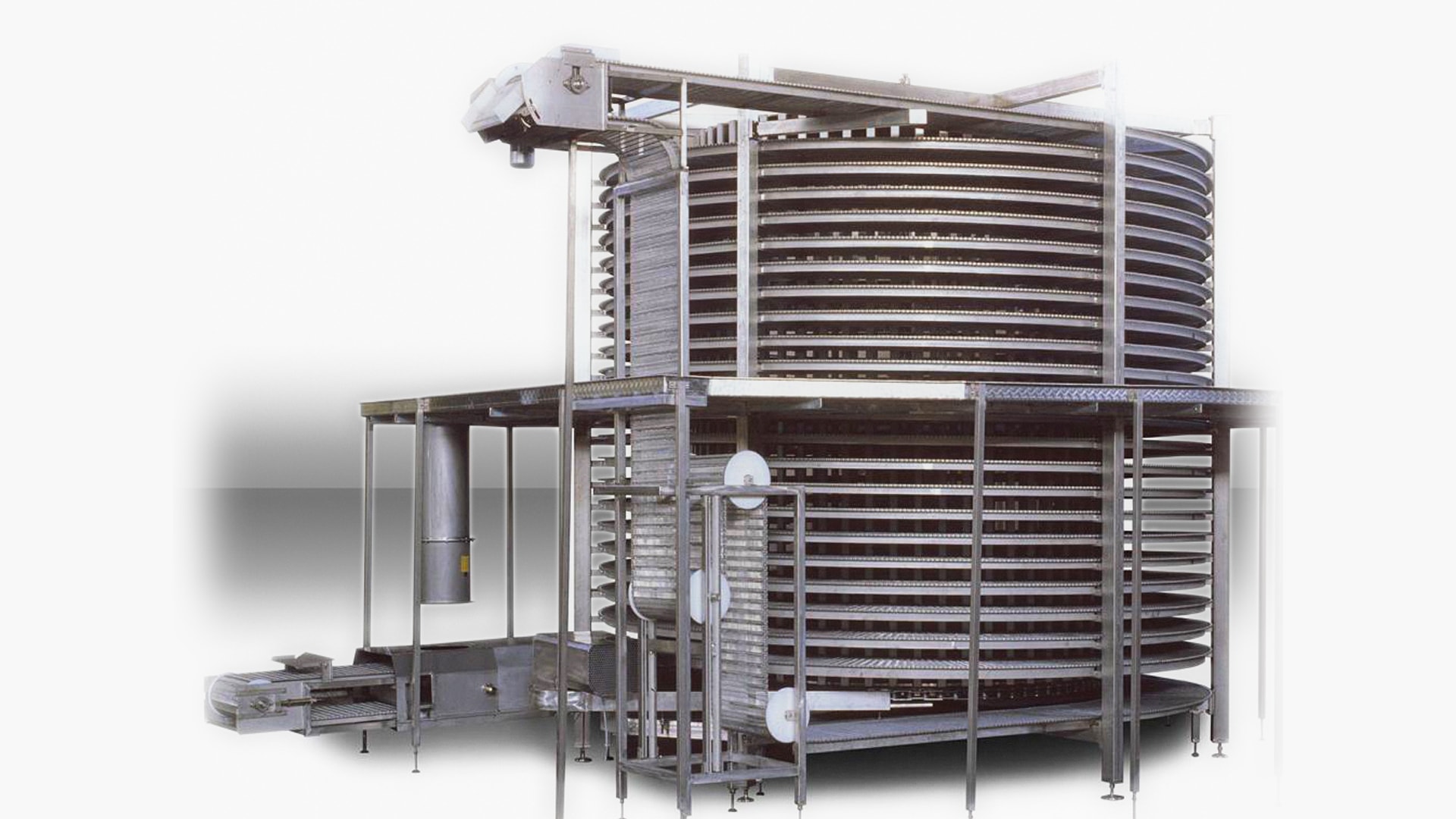
Spirafreeze
-
Industries:
- Baby Food
- Fruits
- Jams & Toppings
- Ketchup & Mayonnaise
- Pasta sauces
- Spreadable creams
- Vegetables
-
Technology:
- Air
Benefits
Ensures uniform freezing, maintaining product quality reducing human error.
Boosts production efficiency by eliminating the need for constant monitoring and intervention.
Reduces labor costs and increases operational cost-effectiveness.
Features
Features
- Enhance operations with a reliable spiral conveyor, minimizing downtime for increased overall efficiency
- Extended belt lifespan, optimal performance, enhancing conveyor system efficiency and cost-effectiveness
- Low cost of spare parts and maintenance activities due to high quality components
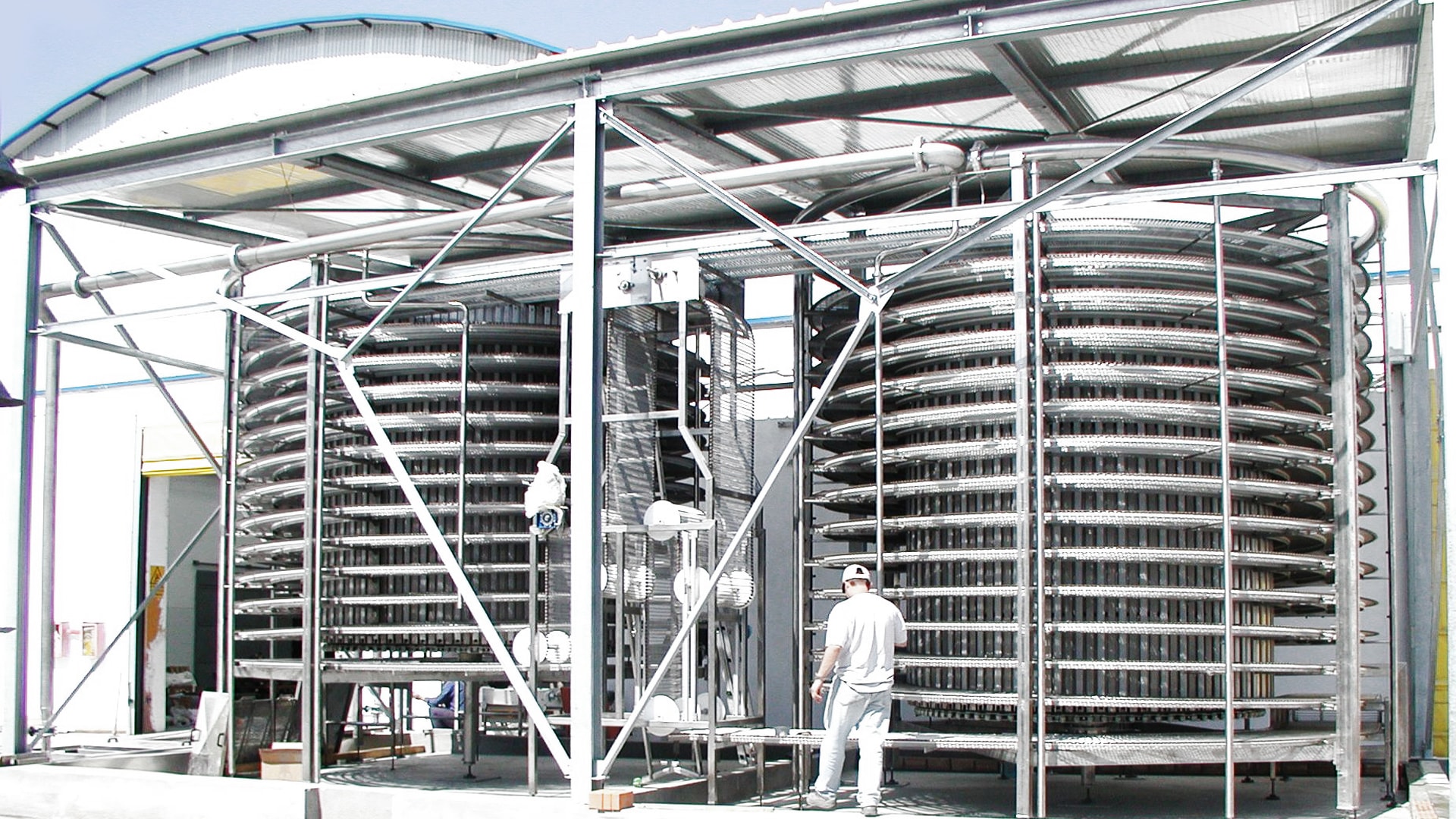
Mecspray MS-R/P
-
Industries:
- Baby Food
- Beverage
- Jams & Toppings
- Ketchup & Mayonnaise
- Other Foods
- Pasta sauces
- Spreadable creams
- Tomato
- Vegetables
-
Min. Capacity:
- 400 Kg/ora
-
Max Capacity:
- 10,000 Kg/ora
-
Technology:
- Water
Benefits
A water recovery and circulation system ensures limited water consumption.
No possibility of product contamination due to the lubrication-free conveyor system.
High mechanical reliability and stability of the spiral conveyor.
Increased heat exchange/production and reduced power consumption thanks to proprietary design of special nozzles for product agitation.
Features
Features
- Stainless steel structures for all water piping and spiral components, including the drum
- Proprietary software for automatic adjustment of belt tension, avoiding tipping
- Reduced belt wear and elongation due to low-tensioned drive system
- Adjustment of the dwell time/speed of the belt by means of variable frequency drives
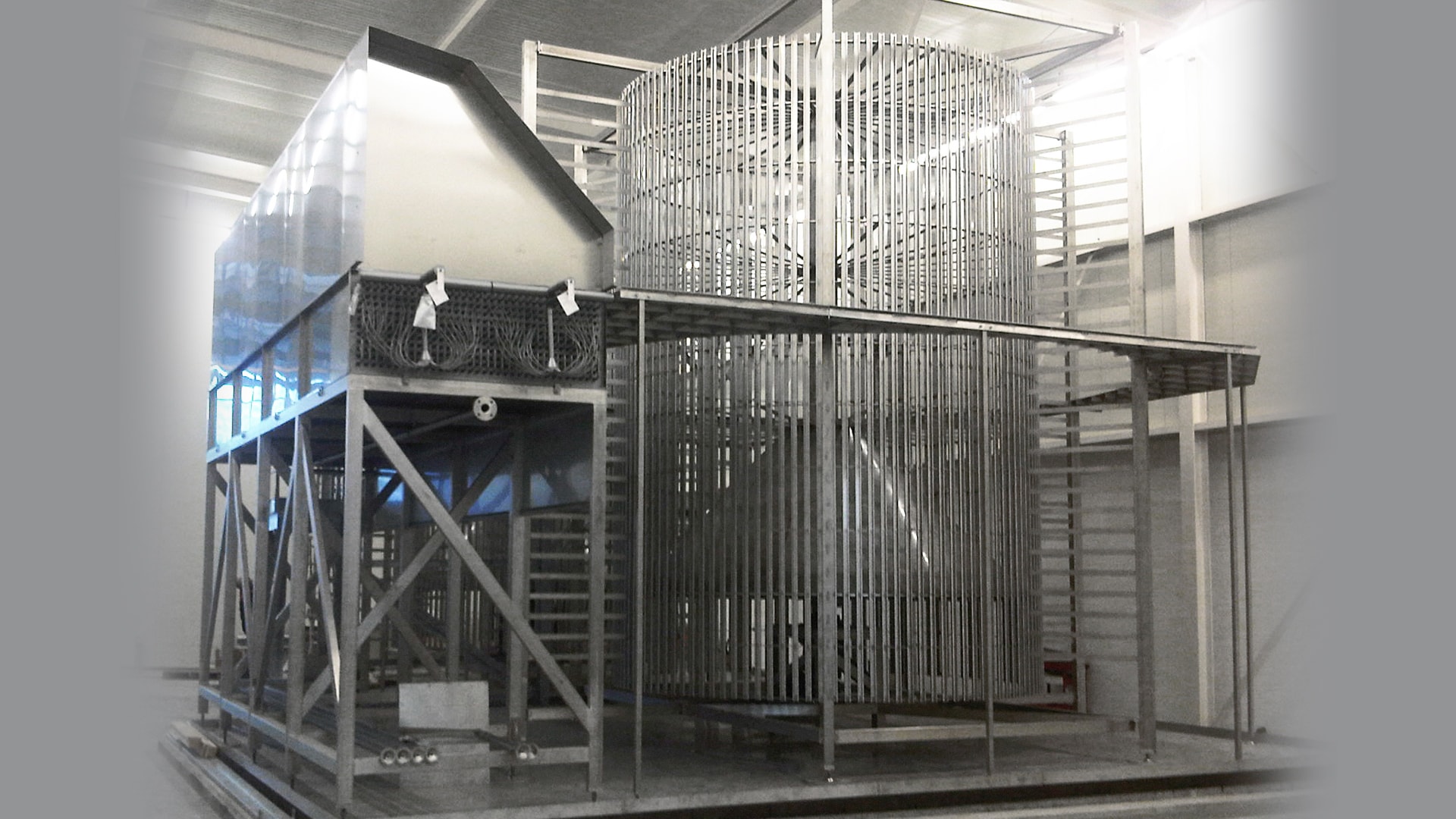
Mecair MA-R/P
-
Industries:
- Baby Food
- Jams & Toppings
- Ketchup & Mayonnaise
- Other Foods
- Pasta sauces
- Spreadable creams
- Tomato
- Vegetables
-
Min. Capacity:
- 400 Kg/ora
-
Max Capacity:
- 3,000 Kg/ora
-
Technology:
- Aria
Benefits
The fast and uniform airflow ensures effective cooling/pasteurization, preserving the quality of the product.
High mechanical reliability and stability of the spiral conveyor.
Low power consumption due to horizontal airflow and vaporizers with very wide fin spacing (coolers).
No possibility of product contamination thanks to the lubrication-free conveyor system.
Features
Features
- Reduced belt wear and elongation due to low-tensioning drive system
- Proprietary software for automatic belt tension adjustment
- All spiral structures, including the drum, are made of stainless steel
- Circulation fans positioned in a dry area to minimize clogging (coolers)
- Long operating cycles due to vaporizers with wide and decreasing fin spacing
No machine found. Please use fewer filters.