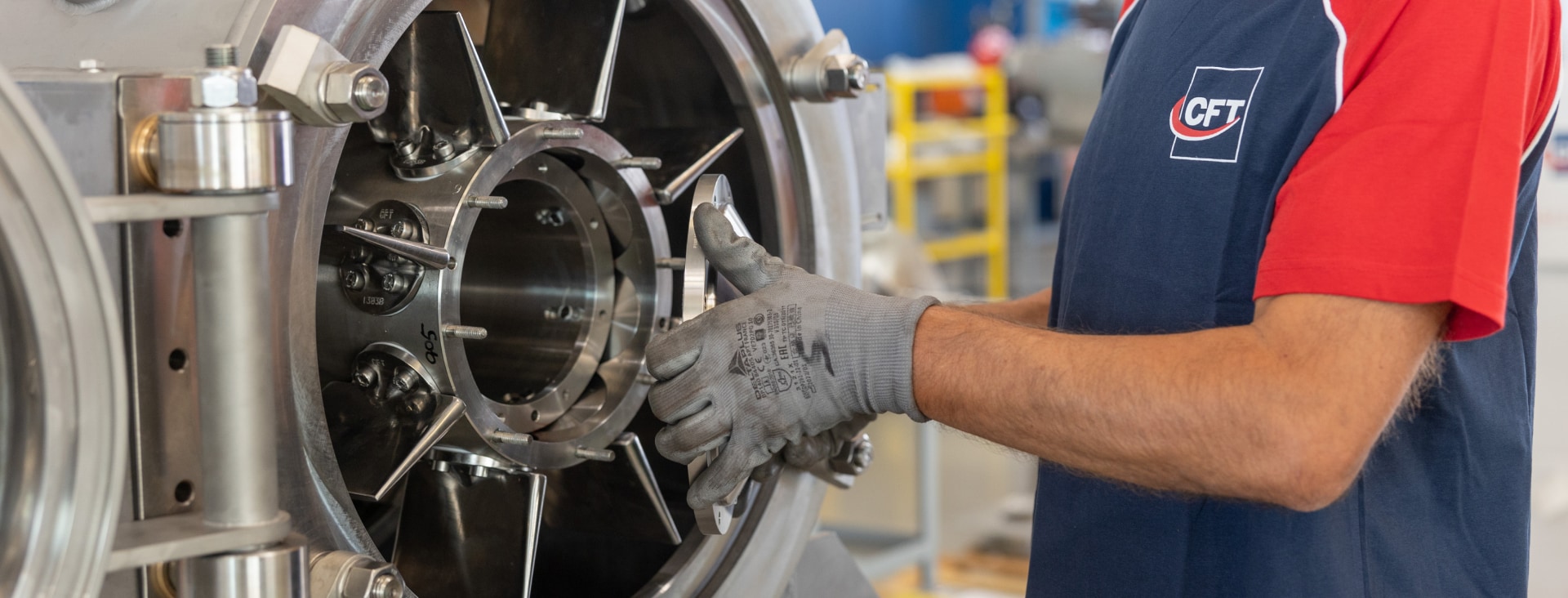
Global Service
A global partner for our customers, wherever they are.
Our global service team offers local expertise, cost-effective support, and a proactive approach tailored to customers’ needs.
Supported Brands
All CFT historical brands can be supported by our service.
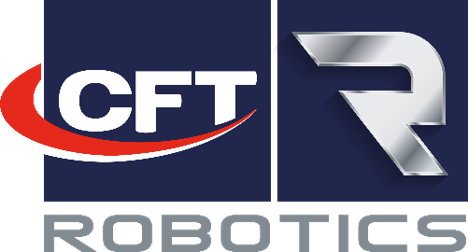

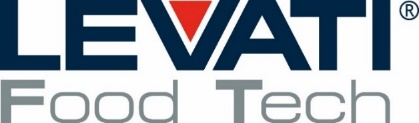

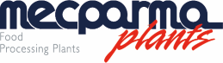

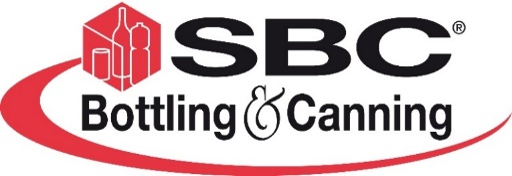
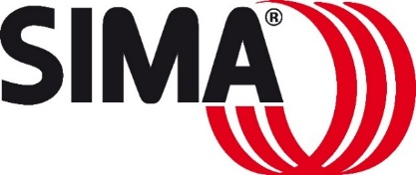
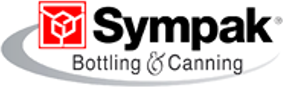
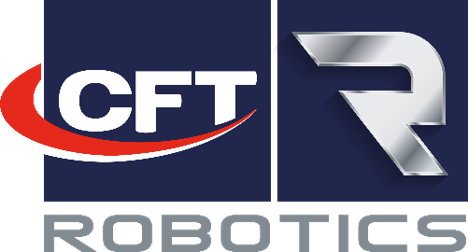

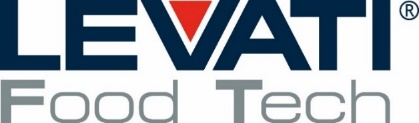

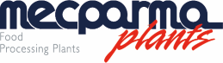

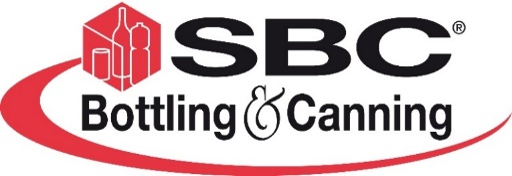
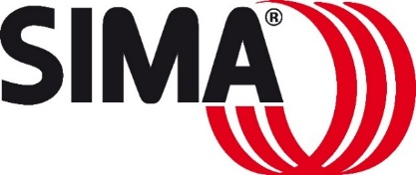
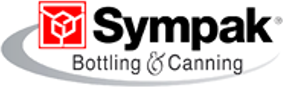
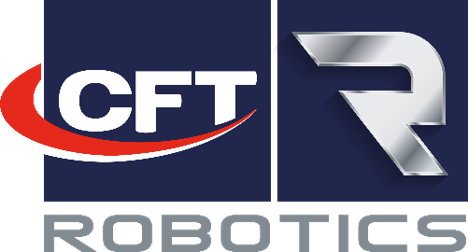

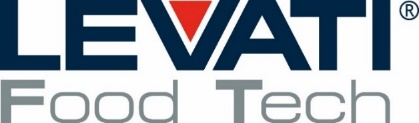

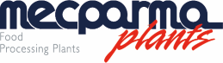

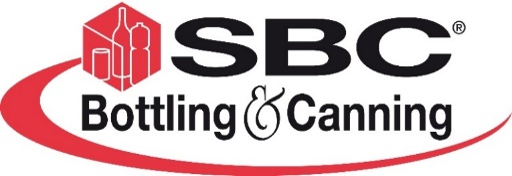
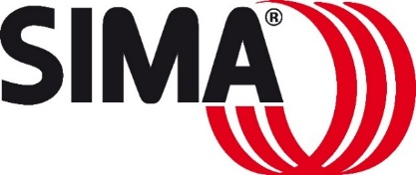
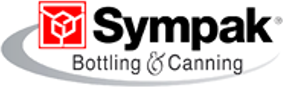
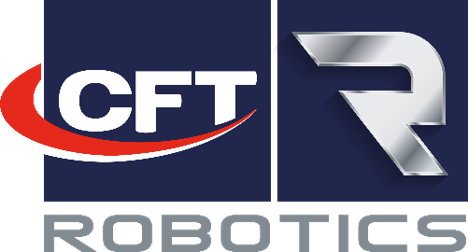

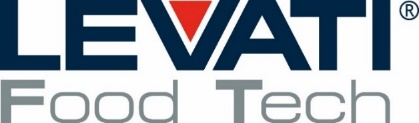

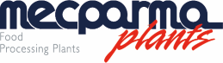

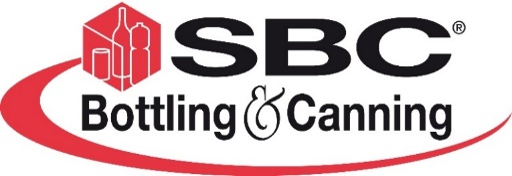
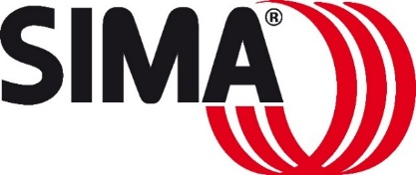
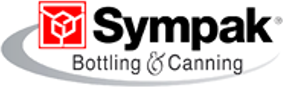
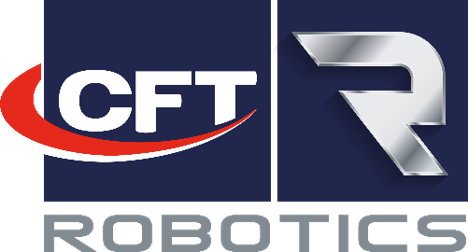

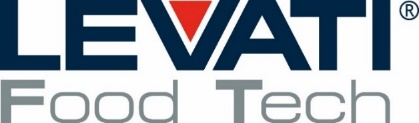

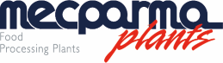

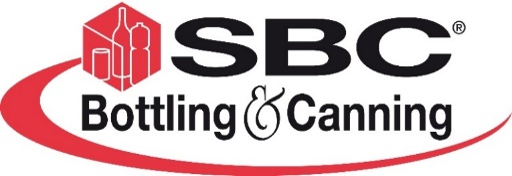
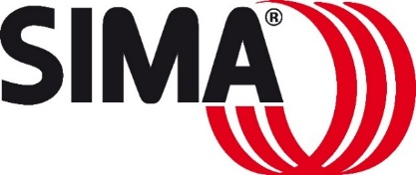
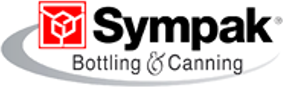
Our services
Spare parts
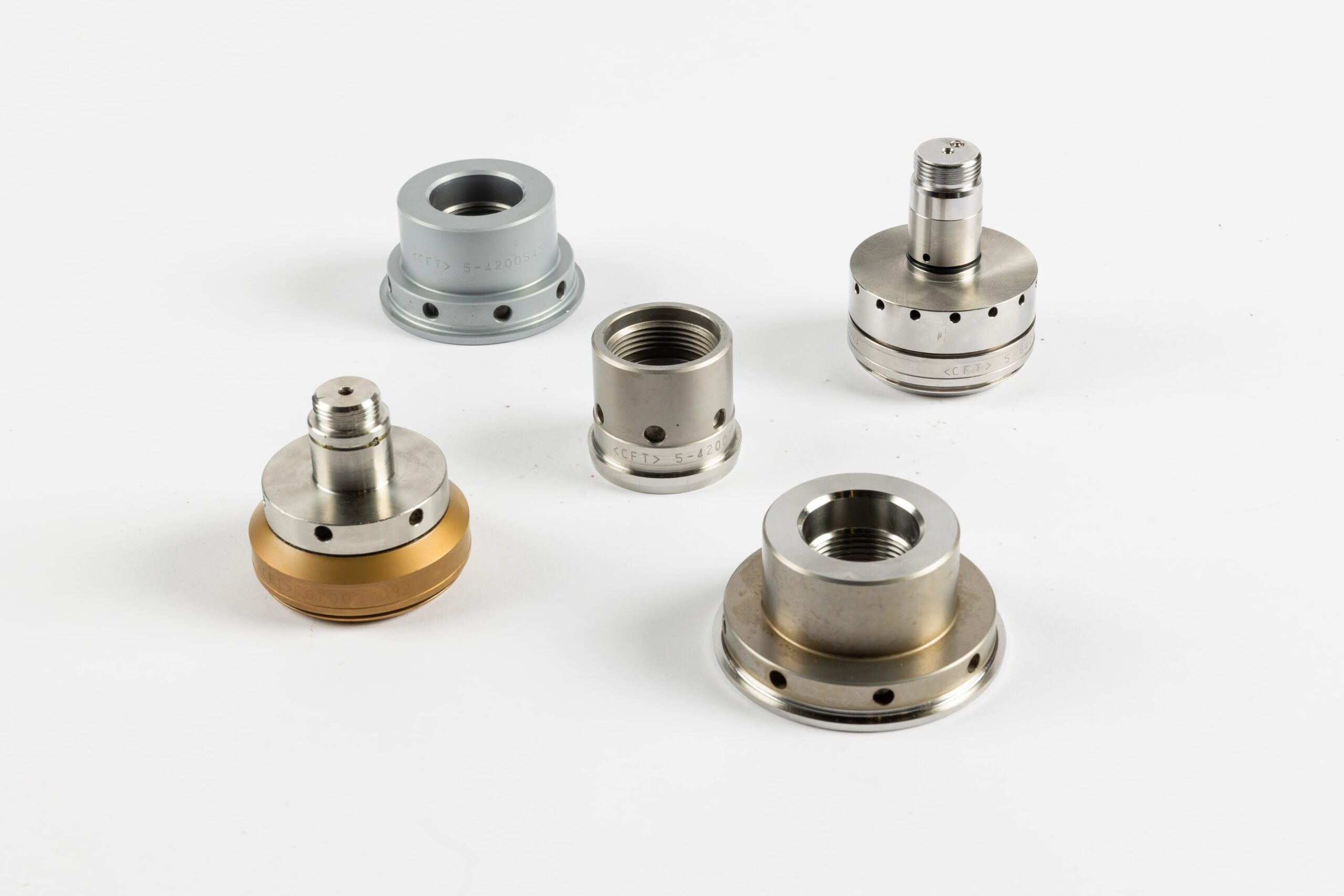
Our worldwide Spare Parts Service provides options for all types of equipment, to guarantee an optimal lifecycle management of all the assets. Our Customer Service Team will help to determine the needed spare parts and make sure they will be available in time. We provide spare parts for:
- CFT Processing equipment
- CFT Packaging equipment
- Third-party equipment included in CFT plants
- Equipment belonging to CFT historical brands
On-Site Maintenance
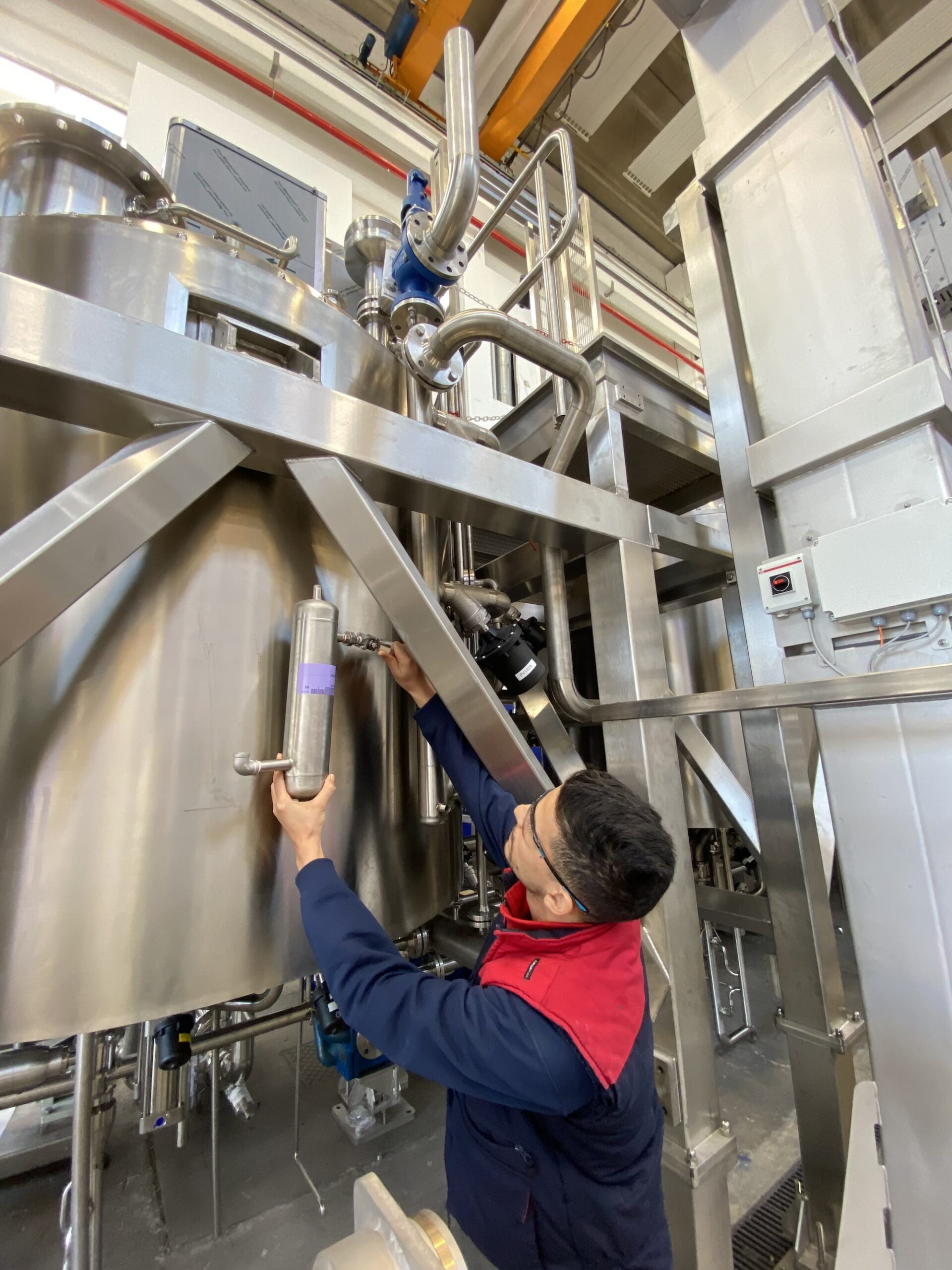
We can deploy well-timed and effective interventions on-site including:
- Diagnostic visits
- Preventive maintenance and monitoring
- Emergency service
- Equipment setting and fine-tuning
Remote Assistance
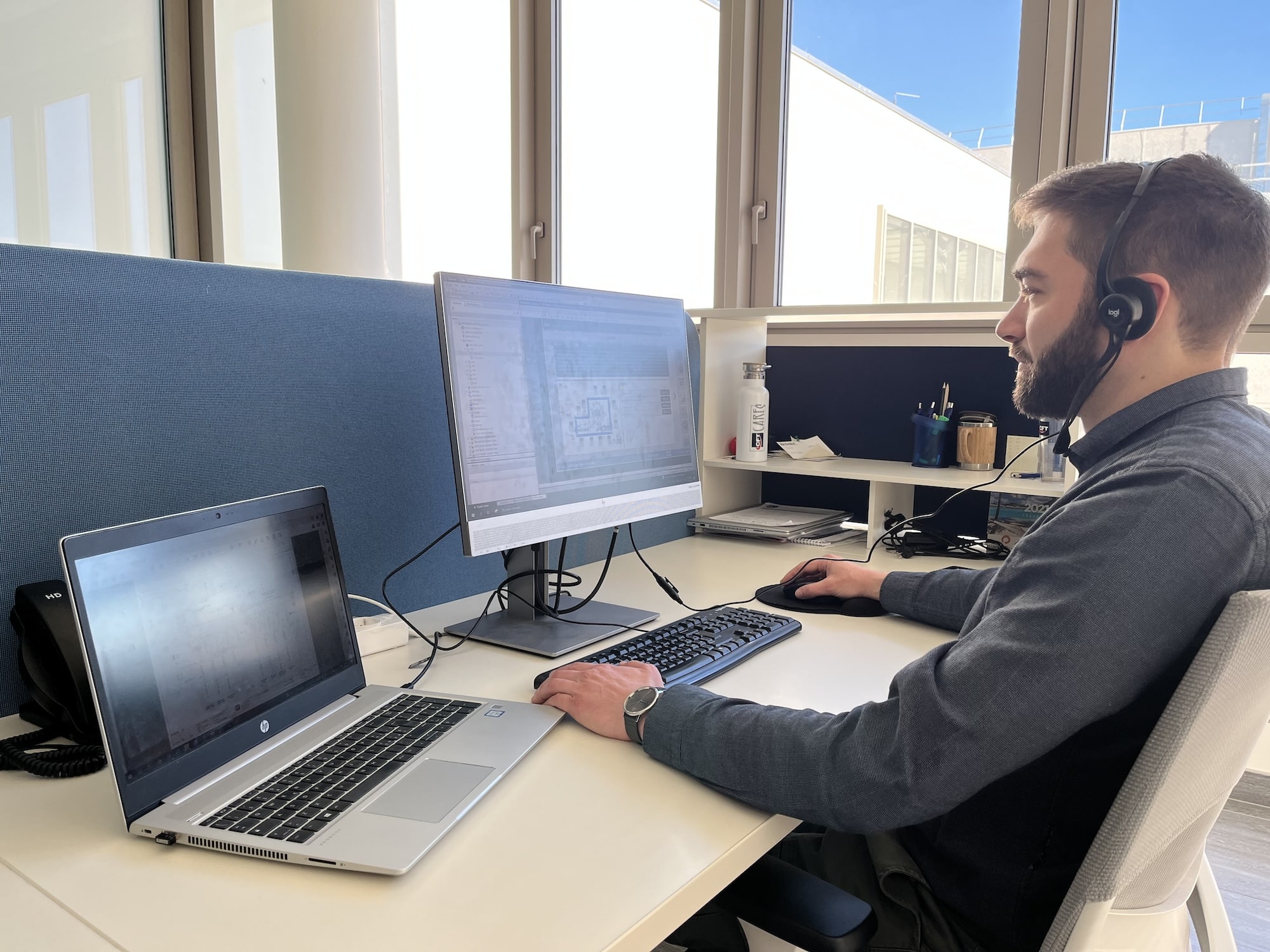
We provide remote support thanks to advanced collaboration and connectivity tools:
- Teleservice for remote troubleshooting and counseling
- Predictive maintenance to remotely foresee potential faults
Upgrades
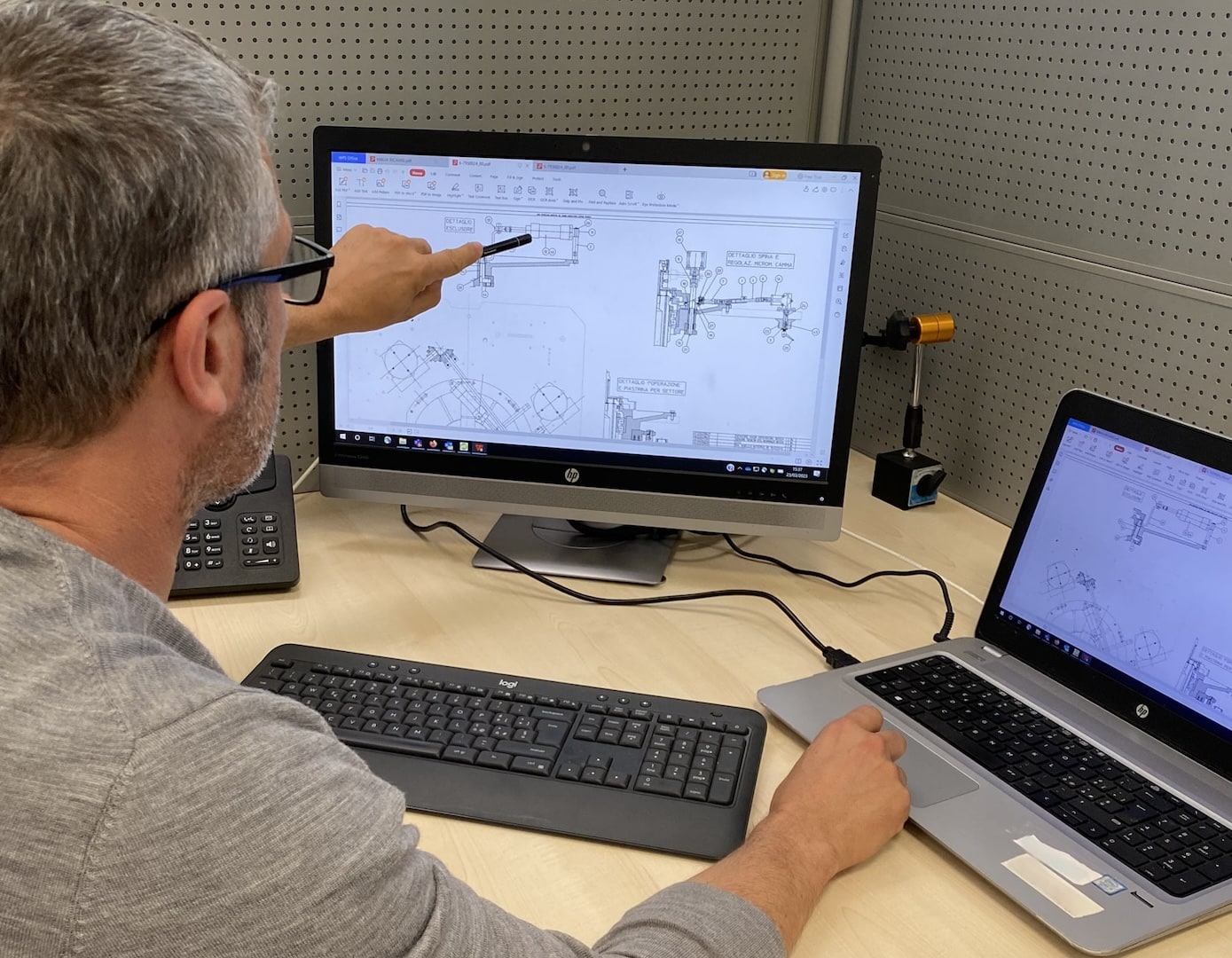
Our Customer Service Experts are always ready to support on the refurbishing and turnaround process of our equipment.
- Overhaul: replacement of worn parts, restoring the original equipment capabilities
- Revamping: replacement of obsolete parts with the latest available technology
- Upgrade: renhancing current capabilities by transforming them into more productive lines
- Line Relocation: consulting and support during the whole process of line relocation
Format change
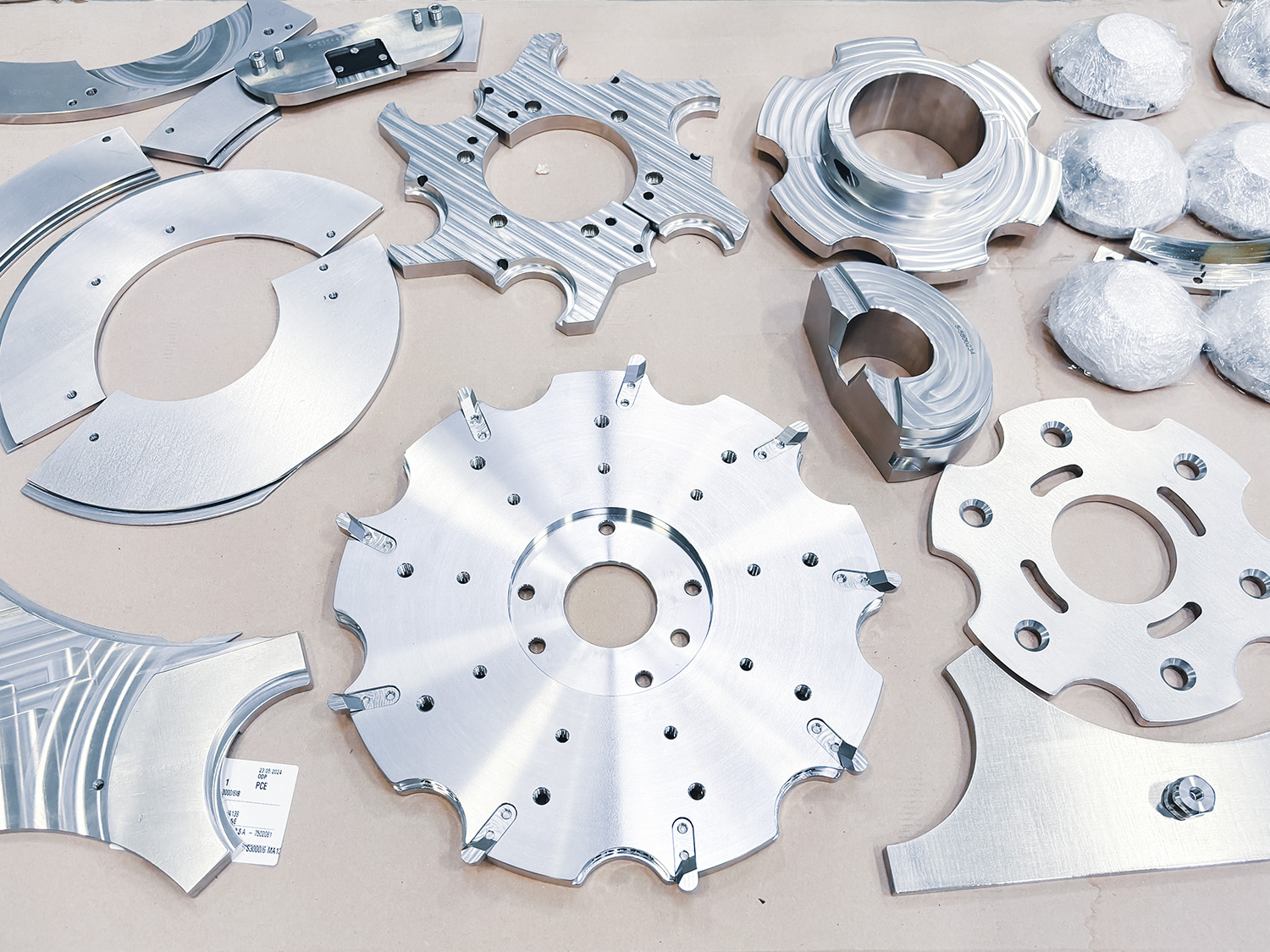
We offer complete format change service for all CFT machines and subcontracting lines, providing flexibility and efficiency in managing different production formats.
- The process involves adding mechanical parts and/or recipes in the software
- We consider format changeover as an upgrade to handle new formats or replace existing ones on the production line
Training

Training programs are designed to make our customers feel comfortable in managing their equipment independently. These programs can be associated with a new installation or a specific need of an existing facility. They can cover the following aspects:
- Safety
- Equipment functions
- Operator procedures
- Maintenance procedures
- Automation procedures
- Troubleshooting
Service Contracts
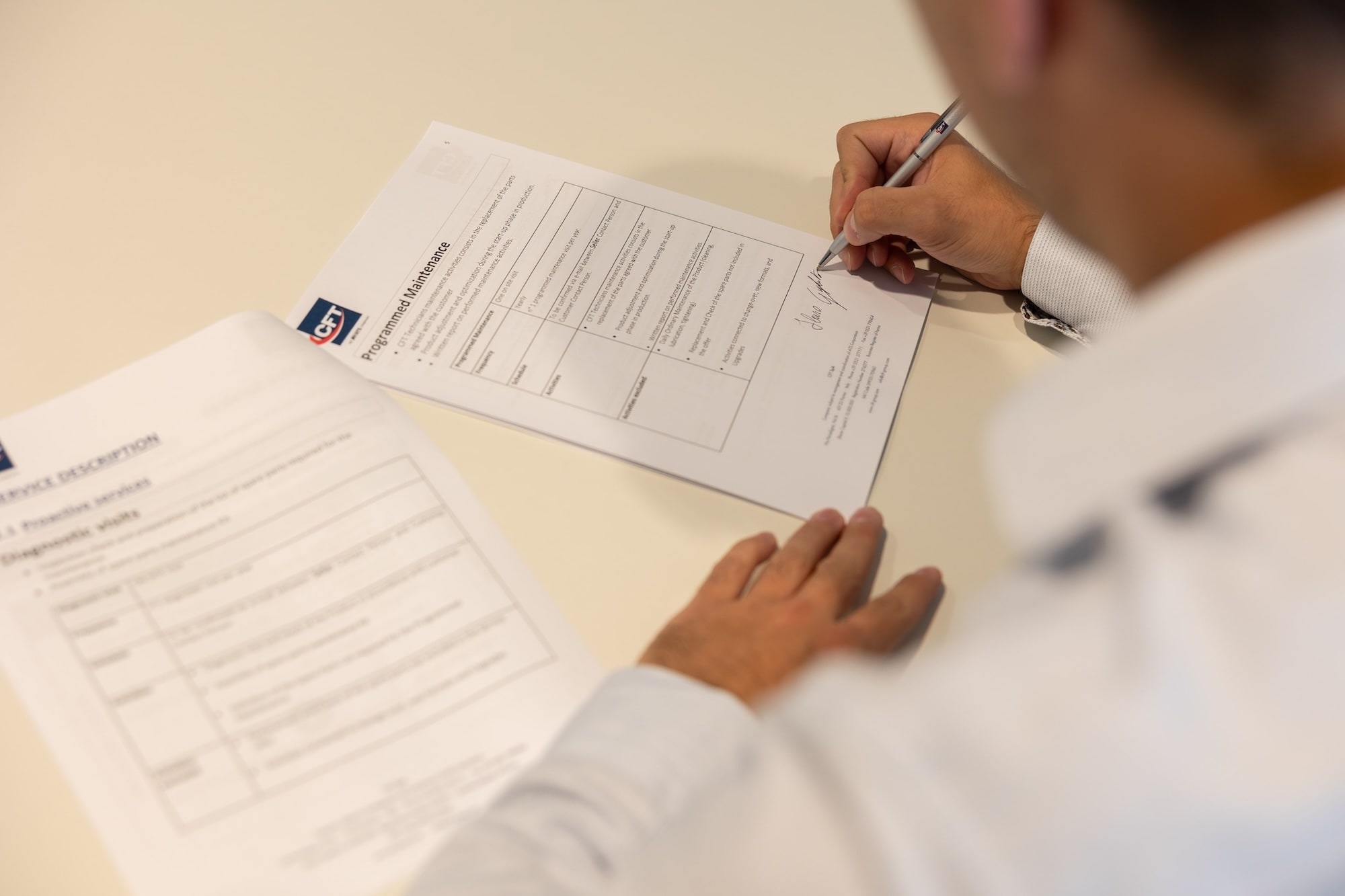
We offer customized and comprehensive assistance programs that can be tailored to any kind of need. These can be contracted either at the time of purchase of a new machine or for existing installations, and can include:
- Overhaul: Diagnostic visit & report, Spare parts maintenance kit, scheduled maintenance
- Overhaul: Remote support service, Emergency on-site assistance availability
Do you need more information?
A global network of service partners
Our service is ready to respond to all the requests in a short time.